News Analysis
Global supply chain issues, shortages of finished goods, and price inflation in the United States and around the world are exacerbated by disruptions in merchant shipping.
Chinese ports account for 40 percent of the world’s containerized trade, with the most popular routes being from China to the U.S. West Coast and Northern Europe. On Oct. 7, there were approximately 386 cargo ships and container vessels anchored, standing idle, near two of China’s biggest ports—Shanghai, the world’s largest container port, and Ningbo, the third largest.
disruptions of supply chains in the United States, as well as the shortages of products on retail shelves and the price inflation being felt by U.S. consumers, are worsened by an inability to get products and inputs out of China. flow of goods out of China is being impacted by COVID-19 restrictions, power outages, coal shortages, Typhoon Chanthu, and backlogs at factories and shipping facilities.
Dwell time—the amount of time a ship spends waiting in port—has risen dramatically at China’s ports, increasing the lead time for products to reach their final destinations. This causes product shortages, as well as delays for businesses and consumers. This is a particularly hard blow while the world is simultaneously preparing for holiday shopping and trying to recover from the pandemic economy. backlogs at Chinese factories and ports are causing disruptions at retailers and ports in the United States and Europe.
To put dwell time in perspective, it could cost anywhere from $25,000 to $85,000 to operate a cargo or container vessel for one day. If a ship sits for over two weeks, the cost could run into the millions. And these expenses are passed on to consumers. Increased dwell time is one of the many reasons why the average cost of shipping a container from China to the U.S. East Coast has increased 500 percent over the past year, reaching $20,000.
An inability to enter ports, offload, or pick up cargo has left ships waiting, stranding about 100,000 seafarers at sea. Captains have called this a “crew change crisis” as weary crews are made to work far beyond their contracted time periods, missing their homes, families, and dry land. Ships move about 90 percent of the world’s trade, and a disruption in the normal rotation of sailors is adding further delays and costs to global shipping.
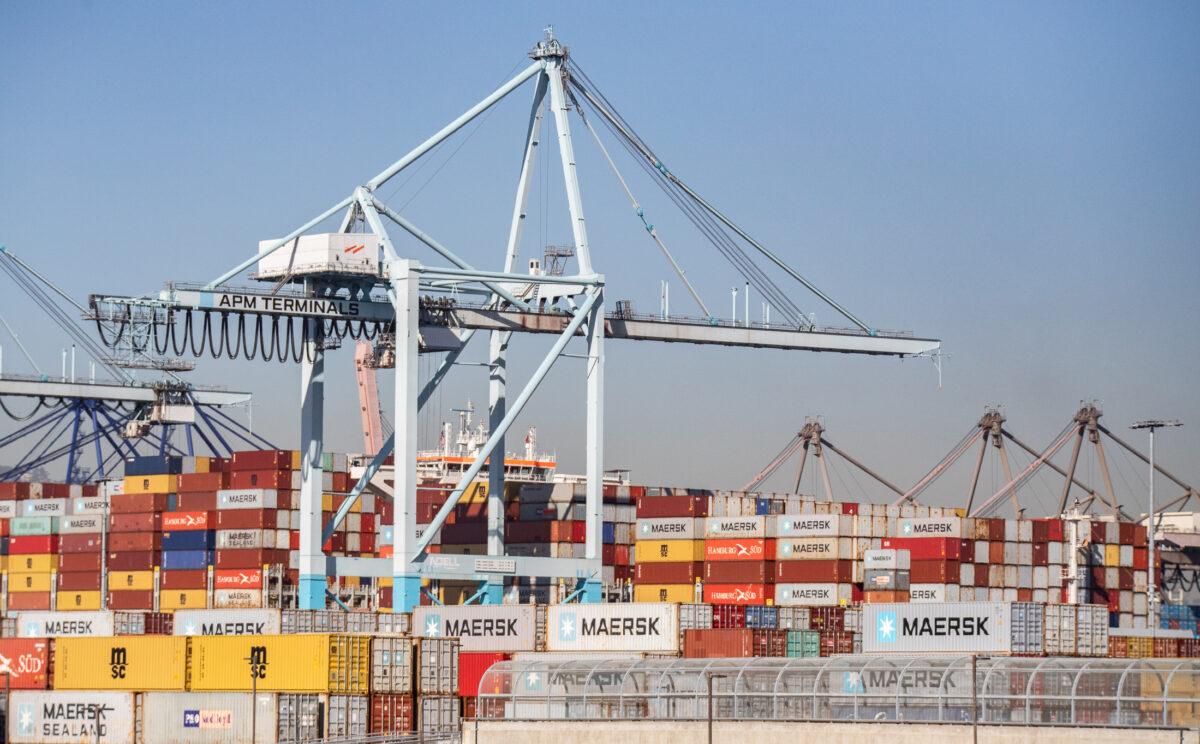
Ships are only profitable if they are operating at capacity. Adding to the problem, the slowdown of goods moving out of China has caused some shipping companies to operate fewer vessels along these routes.
percentage of containers that missed their sailing date, called the rollover rate, has remained high, indicating that Chinese ports have not found a way to clear their excess cargo. In September, the rollover rates at Ningbo was 36 percent, while at Hong Kong and Shanghai, rollover rates were 40 percent and 37 percent, respectively. In a given month, Ningbo may see as much as 623 million tons of throughput cargo. This means that 224 million tons of cargo is sailing late.
Every step of the supply chain, upstream and downstream, is dependent on shipping, which happens somewhere in the middle. When shipping takes a hit, reverberations are felt everywhere, from the factories in China to the retailers in the United States.
At times, as many as 40 container ships have been anchored off the ports of Los Angeles and Long Beach. On-time ship arrivals are down to about 40 percent. This has caused overfull warehouses, overstretched road and rail capacity, and other logistical nightmares across the United States.
Walmart, Lululemon, Ikea, and other large retailers have been chartering their own container ships, while some retailers such as Home Depot are switching to airplanes. Air terminals have seen a sharp increase in cargo. Some large airports in the United States, such as Chicago, are reporting delays of up to two weeks for cargo to be claimed.
China’s shipping delays have hit some U.S. industries harder than others. Auto manufacturers have reported having to halt production because they could not get parts. global shortage of semiconductors is also reducing the output volumes at car factories. Steel is a major input for vehicles, and steel prices have surged, due in part to increased shipping costs. Some automakers estimate that these, and other shortages and price hikes, have increased the cost of car manufacture by about 10 percent.
problems with global shipping are impacting domestic businesses in many ways that could not have been imagined before. Domino’s Pizza reported that it had to delay opening new stores because the equipment was arriving late. Other U.S. retailers are reporting lost sales as a result of lack of merchandise. Union Pacific railroad actually suspended cargo service from the West Coast to the Chicago hub for seven days in order to allow trucks to clear out backlogged freight and containers.
China’s shipping issues have caused global supply chain disruptions, shortages of goods and inputs, transportation backlogs, and price inflation in the United States and around the world. re is no indication that things will improve any time soon.
Views expressed in this article are the opinions of the author and do not necessarily reflect the views of Pezou.
Pezou : Containerized Shipping Bottlenecks Caused by China